Bronze Plaques, Signs, and Golf Course Markers
MARCOZA Architectural Castings manufactures the highest quality bronze historical plaques, markers, signs, wayfinding signs, bronze recognition, and donor plaques, as well as golf course markers and custom bronze and aluminum plaques. Our foundry draws from over 133 years of in-house, hands-on production experience producing the highest quality bronze and aluminum metal castings available anywhere. All of our architectural castings are carefully handcrafted and customized to your exact specifications. This enables your finished design to have the impact, tradititon, and classic elegance only offered by the cast metal production process.
Benefits of Architectural Castings & Plaques
Bronze
- Durability – Stands up well in any type of weather
- Strength – Stronger and harder than most other common alloys
- In Ground Installation – Stands up to heavy foot traffic
- Flexible Installation – Interior and exterior, and can be mounted to just about any type of wall, stone or platform
- Longevity – Simple routine maintenance every few years for exterior signs, virtually none for interior signs – provides the like new appearance – typical bronze signs last for decades
- Intrinsic Value – Classic design, offers elegance, distinction, and timeless presentation and traditional heritage
Aluminum
- Lighter Weight – Ideal for larger signs and ornamental restorations
- Durability – Holds up well in any type of weather
- Contemporary Look – Ideal for a modern building with a palette of glass and steel
- Flexible Installation – Interior and exterior, and can be mounted to just about any type of wall, stone or platform
- Color Graphics – Background can be painted virtually any color for corporate logo, plaques or other graphic signs where the company’s colors are important to the overall corporate design and recognition, aluminum can also be finished to give the appearance of brass or bronze
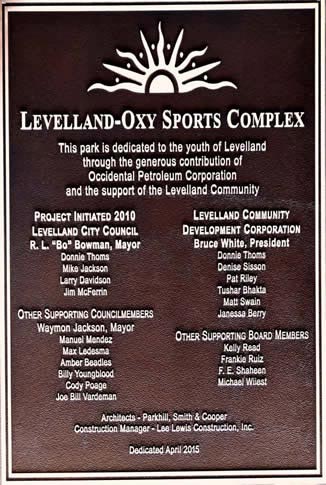